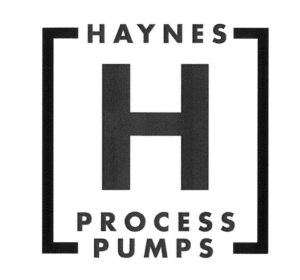
Kerr Pump and Supply, established in 1905 and located in suburban Detroit, is the most respected name in vertical process pumps. Our innovative, heavy duty, time proven design combines advanced hydraulic engineering with mechanical craftsmanship to meet a wide range of industrial applications. Each pump is engineered with the objective of performing on a continuous duty operation with the longest life and a minimum amount of maintenance. With domestically poured castings, in-house machining and assembly, we proudly place a “Made in America” label on all our Haynes Pumps.
Our Haynes pumps handle the varied requirements of metal finishing, parts washing, and industrial chemical process industries. Simplicity of design eliminates pump priming, troublesome shaft sealing problems and the inherent maintenance costs of mechanical seals.
Outstanding quality features included in every pump contributes to longer pump life. Each component has a machined registered fit at all assembly points to assure positive alignment and vibration free service. Haynes pumps are a sound investment in the best available technology – at no additional cost.
HAYNES VERTICAL CANTILEVER PUMPS – MODELS 6500 AND 6600
Advantages
- Externally adjusted impeller- always primed
- Minimum maintenance costs
- No stuffing box leakage
- Lower installation costs
- Less space required
Capabilities
- Capabilities to 3000 GPM
- Heads to 240 feet
- Temperatures to 180°F
- Cast iron and alloy construction
- Flexibility on pump extensions and deliveries
- Double volute casings for reduced side load
Applications
- Parts washers
- Spray booths
- Paint systems Coolants
- Plating
- Phosphatizing
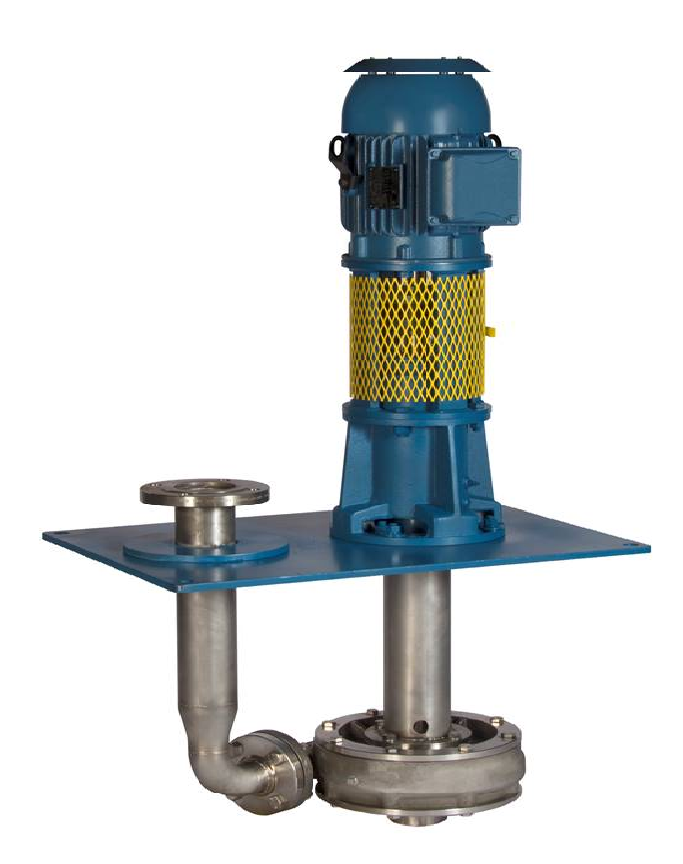
External Impeller Adjustment – Impeller can be adjusted to change running clearance, making it easy to restore near original pump performance without dismantling the pump.
Impeller – Semi-open with extra heavy vanes for outstanding performance and resistance to wear. Allows some small solids handling capability. Wiper vanes on backside of shroud prevent material accumulation and pump binding.
Throttle Bushing & Slinger – Restricts liquid from entering the column area and prevents liquid from traveling up the shaft.
Bearings – Precision ground, heavy duty grease lubricated bearings are mounted above the coverplate for ease of maintenance and sized to exceed maximum pump loads.
Dual Shaft Seals – Designed to prevent dirt, vapors, and moisture from entering lower bearing area.
Shaft – Heavy duty shaft of high strength materials is turned, ground, polished, and sized with the optimum diameter and bearing span to eliminate deflection problems.
Pump Down Recirculation Line – Creates a liquid seal in the throttle bushing area. This optional service promotes tank pump down capabilities.
Powerframes – Two sizes handle the whole line, which means less parts to stock
Materials of Construction – Pumps are available in all iron, s.s. fitted, 316 s.s., and carpenter 20 construction below the coverplate.
HAYNES HORIZONTAL CENTRIFUGAL PROCESS PUMPS – BACK PULLOUT
Capabilities
- Sizes 1-1/2″ to 8″
- Capacities 40 to 3,000 GPM
- Heads to 230
- Materials: 316 s.s. Carpenter 20, and all iron
Applications
- Spray Booths
- Filtration Systems
- Industrial Spray Washers
- Phosphate Systems
- Paint Systems
- Coolant Systems
Haynes Model 6050 features:
Heavy Duty Casting – Precision machined
Extra Heavy Duty Shaft – For minimum deflection
External Impeller Adjustment – For ease of maintenance
4-piece casing – With machined fits
Impeller – Semi open and Keyed to shaft with precision taper fit
Bearings – Two heavy duty bearings: 1 double row “thrust” & single row “radial” designed for longer life
Grease Seals – To totally seal out foreign material
Stuffing Box – Furnished as standard with packing & lantern ring. Same stuffing box will take single or double mechanical seals
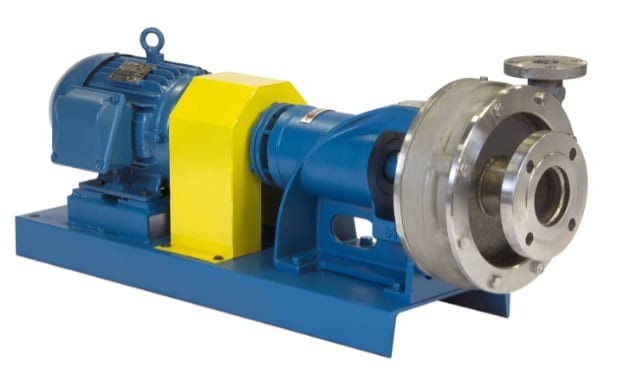