Liquid Pumps
There are many different types of liquid pumps. This briefly describes how each works and the typical applications. Kerr Pump & Supply can save you time by consulting with you on your specific application’s needs. There are often multiple pumping solutions – each one with it’s own set of advantages and disadvantages – that our Sales Engineers can discuss.
Air Operated Double Diaphragm Pumps (AODD) can handle water to 90 percent solids and used mostly in industries like water treatment or food processing.
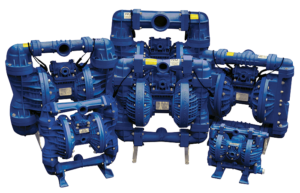
ANSI pumps are centrifugal pumps that are horizontal, end suction, single stage that are comparable in size and identical in interface and envelope dimensions regardless of manufacturer.
Booster pumps increase the pressure of a fluid may be used for increasing gas pressure, transferring high pressure gas, charging gas cylinders and scavenging.
Canned Motor Pumps have an electric motor where the rotor winding is encapsulated and is immersed in liquid and the rotor shaft has the impeller at the end.
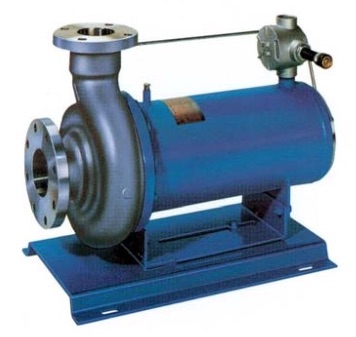
Centrifugal pumps operate by having the fluid enter the pump impeller along the rotating axis, being accelerated by the impeller, flowing radially out into the diffuser or volute chamber, where the fluid exits.
Chemical pumps like the name suggests carries chemicals and are resistant to corrosive and abrasive liquids.
Circumferential piston pumps have two displacement pumps that are able to transport very low viscosity liquids at high discharge pressure for food, dairy, beverage and other hygienic applications.
Condensate units are used to pump the condensate produced in an HVAC, refrigeration, condensing boiler furnace or steam system.
De-aerators are most often used to remove oxygen and other dissolved gases from the feed water to steam generating boilers.
De-watering pumps remove water from solid material by a solid liquid separation processes.
Drum pump is used for barrels, tanks, IBCs and drums that contain liquids that are too heavy for tipping over to empty.
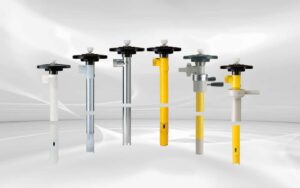
Engine driven pumps are pressure compensated, variable displacement axial piston pump capable of varying volumes of fluid delivered to maintain hydraulic system pressure.
End suction pumps are the most common types of centrifugal pumps. Usually single stage pumps and are the most affordable type of centrifugal pumps. They have a casing with the suction coming in one end and the discharge coming out the top.
External gear pumps are used as lubrication in the pump engines and provide more precise measurements of liquid going through the pump and greater flow control and are run quietly.
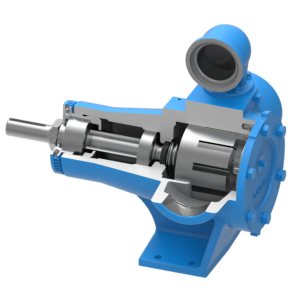
Fire pump intakes are either connected to public water supply piping or a static water source and provide water at a higher pressure.
Grinder pumps finely grind sewage and pump it into elevated destinations.
Internal gear pumps are the same as an external gear pump except it uses both internal and external gears.
Jockey pump is a small pump connected to a fire sprinkler system to maintain pressure in the sprinkler pipes.
Magnetic Drive centrifugal pump has the wet end and motor as two separate contained parts connected by only a motor bracket. A drive magnet is attached at the end of the motor shaft and the magnet rotates in synchronization with the impeller that is fixed on another magnet.
Metering pumps allow for fluid metering during the process flow to control exact quantities especially in fluid dosing applications.
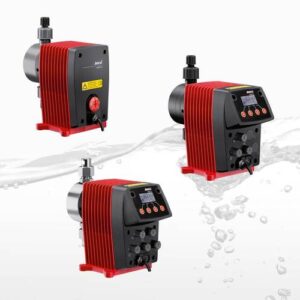
Plunger / Piston Pump is a type of displacement pump where the seal reciprocates with the piston while a plunger pump is where the seal is stationary and a smooth cylindrical plunger slides through the seal.
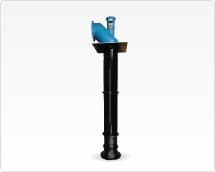
Propeller pump is a high flow, low lift impeller type device that features a linear flow path and it can installed vertically, horizontally and angled orientation and has the motor above the water level with the impeller below.
Process pumps are used to move fluids and has many types depending on application. Can be used to pump corrosive or abrasive fluids.
Progressive Cavity pumps transfer fluid through the pump in a sequence of small fixed shape cavities as the rotor turns.
Pump transfer stations are holding or processing sites for temporary deposition of waste.
Regenerative pumps fill the need between centrifugal and positive displacement designs that combines both the high discharge pressure of displacement types with the flexible operation of centrifugals.
Rotary Lobe pumps reverse flow direction at any time can run dry for long periods of time can handle solid objects, and highly viscous liquids.
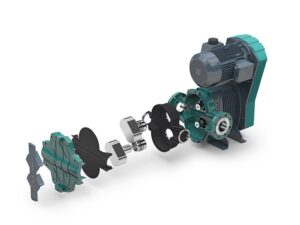
Sand, Sludge, Slurry pumps are for large quantities of water that contains hard and soft solids like mud, sand and sludge. They are also portable.
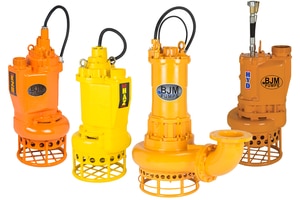
Self-priming pumps are designed to lift water from a certain level below the pump suction without having to fill the suction piping with liquid. The air/water separation is what makes the self-primer unique. Some are capable of handling solids along with liquids.
Sewage pumps are used to move solids and liquids between locations uphill and will typically sit in a sewage basin.
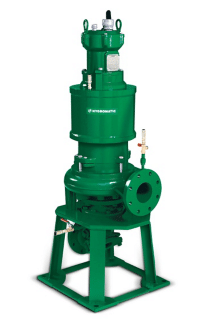
Shredder pumps are used to shear down debris that could cause clogs before pumping.
Split case pumps allows for the rotor to be removed without moving the motor, less shaft deflection, higher efficiency and high nozzle loads.
Submersible pump is hermetically sealed motor close coupled to the pump body. It prevents pump cavitation which is caused by high elevation difference between pump and the fluid surface.
Sump pump is used to remove water that has accumulated in a water collecting sump basin.

Turbine pumps use impellers with radially oriented teeth that move the fluid and are preferred in applications where high head, low flow, and compact design are desired.
Vane pumps operate with low flow pulsation and makes it quiet while still having high speed. They also can be used with different levels of viscosity
Vertical pumps utilize a shaft and bearing support that allows the volute to hang in sump while the bearings are outside the sump. Vertical Multi-stage pumps contain two or more impellers.
Vertical seal-less centrifugal pump has the impeller shaft contained in a sealed pressurized containment shell that contains the process fluid. Leakage is prevented by the use of static sealing technology.
Liquid Pumps Manufacturers
View all of our Pump Manufacturers