In this article, we compare the differences between variable speed and fixed speed, as well as how to improve the efficiency of your pump system. Published data is used to emphasize those differences and why one system may be more beneficial in today’s era.
Variable Speed Pump vs. Fixed Speed Pump
What is the difference between a variable speed pump and a fixed speed pump? In general, a fixed speed pump motor operates at its rated speed regardless of the flow conditions. The pressure that is being produced by the pump is determined by the amount of water that is being demanded by the application.
Variable speed booster pumps have several advantages over constant speed pumps including:
- elimination of energy losses of pressure reducing valves and the high-head conditions as flow decreases
- extended motor life without constantly being on
- reduced cost of operation over the pump lifecycle
- extended motor bearing and pump seal life
- minimized water hammer in the system
- new pump efficiency rates as high as 80%
Variable speed pumps are much more common than the older constant speed split case, vertical turbine, and end suction pumps.
What Is a Variable Speed Booster Pumping System?
In most applications where water is used, whether commercial or industrial, the demand for water pressure changes at different times of the day. A variable speed water pressure booster pump is designed to adjust the water output and keep the water pressure constant. By using a variable speed drive (VSD), a variable speed pressure booster pump can continuously optimize pump speed and power consumption and, at the same time, maintain constant pump outlet pressure.
Benefits of Using Variable Speed Drives
Consistent water pressure is a must for correct operations of industrial and manufacturing machinery. At the same time, water distribution systems are compelled to increase efficiency, decrease water wastage, and improve the reliability of the installed systems to reduce ongoing maintenance and repair costs.
Given these realities, what are the benefits of using variable speed drives on pumping system? VSDs are one of the best ways to improve the mechanics of water distribution systems. Most of the benefits can be categorized into three key areas:
- Reliability: Variable speed booster pumps do not run on a stop/start cycle, and they often run at lower speeds. The result is reduced stress on the pump and greater reliability. With a longer life cycle and decreased downtime, cost of maintenance can also be reduced.
- Energy efficiency: According to the U.S. Department of Energy, a variable speed water booster pump with pressure sensors to maintain constant pressure output can be up to 30% more efficient than traditional technologies.
- Control Management: A variable speed water booster pump can maintain constant, reliable water pressure even in challenging environments like high-rise buildings. Digital technology also makes it easier to collect data and modify the pressure supply (depending on load and preference).
All of these elements add up to reducing the total cost of ownership for the variable speed booster pump system.
How Do Variable Speed Pumps Work?
In a constant speed booster pumping system, the pump does not change speed. Instead, pressure reducing valves throttle head pressure through friction and resistance. A variable speed booster pumping system allows for varying water pressures and flow rates to accommodate the demand of the building or application at any given time. The fact is that 80% of the time, a booster pump operates at 20% capacity or less. During low demand, a variable speed control slows the pump speed so a variable speed pressure booster pump can take advantage of pump and fan affinity laws.
When the speed of the motor is reduced, power is reduced. On a pump curve, generally the flow and head are changing at the same time. As flow increases, pressure capacity drops, and vice versa. When a variable speed water pressure booster pump is used, it reduces speed to match a constant discharge pressure by slowing the pump down as the flow decreases and the potential pump pressure increases. As the pump slows, based on affinity laws, the energy consumed is reduced by a factor of eight.
How do you control pump speed in a VSD system?
In some cases, the controller is a simple, manually operated control panel. In other cases, it can also be controlled by a more complex programmable logic controller (PLC) combined with a Variable Frequency Drive (VFD) that varies the frequency to the pump motor, speeding it up or slowing it down based on input from system variables such as flow, level or pressure. For automated control of the variable speed pressure booster pump, sensors gather data to indicated when pump speed needs to be increased.
What Is the Minimum VFD Speed for Pumps?
The minimum variable frequency drive (VFD) speed for pumps to maintain flow depends on the system curve, especially the amount of static head, which varies depending on the application. To determine the minimum VFD speed for a pump, you need to analyze several parameters,
including velocity in the largest sections of the pipe, minimum flow for the pump based on the system curve, and motor cooling. From that, the minimum flow can be computed based on the most conservative limiting factor.
How to Control Variable Speed Pump Systems
How do you control a variable speed pump? VFDs will speed up or slow down in reaction to changes in system pressure via a pressure transducer. The VFD adjusts the pump’s output pressure to satisfy a fixed system pressure.
Often pressure sensors are used to measure the outlet pressure and send that data to the VFD so the speed of the pump can be adjusted accordingly. Some systems rely on another pressure switch to prevent the pump from outputting extreme pressure. In smaller pressure booster pumping systems, the pressure sensor is normally placed at the furthest possible location. For a larger VSD booster pump system, multiple sensors can be used, each placed in a critical area of the system, or different set points can be established depending on the number of pumps operating.
Often a custom control panel is part of the solution to control variable speed pumps and ensure optimum performance of your variable speed sump system.
Booster Pump Flow Rate
Any water booster pump operates by increasing water pressure, which forces the water to flow faster through hydraulic lines. However, in any pumping situation, flow velocity decreases as the pressure necessary for the movement of water increases. Booster pumps can provide most water at the highest flow rate at low pressure. If the water flows from the pump without restriction, it moves with a greater flow rate.
Are Variable Speed Pumps Worth It?
For most applications, the question boils down to this: do variable speed pumps save money? In comparison with fixed speed pumps, generally the initial cost can be quickly recovered. One study in the Journal of Water Supply: Research and Technology-Aqua found that the potential energy cost savings realized by installing variable speed drives instead of fixed speed pumps is about 20%. Since power consumption accounts for around 85% of all costs over the lifecycle of a pump, even minor efficiency improvements amount to sizeable savings. Variable speed pump systems also reduce maintenance cost and provide significant reduction in leakage as well.
Advantages of IMO HD2 VFD’s for Pressure Regulation
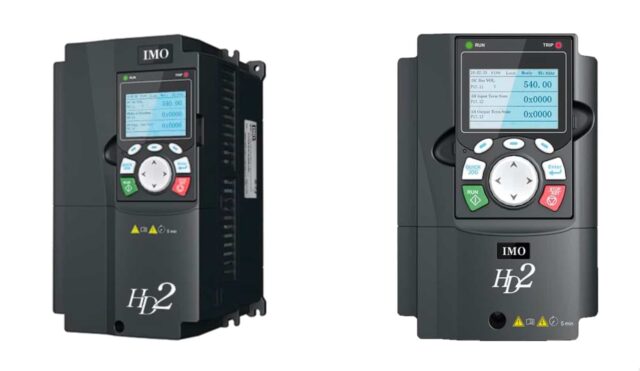
Kerr Pump & Supply offers the IMO VFD’s as a solution for pressure regulation. IMO’s HD2 VFDs provide several key features that simplify a variable speed booster pumping system and while enabling additional control and greater efficiency. Features include:
- Sleep mode. The sleep mode function enables the drive to conserve energy when the system doesn’t require pressurization.
- Programmable inputs. These digital and analog inputs are able to interface with feedback devices such as transducers, BMS, or PLC-control for precise speed control.
- Bypass or hand/off-auto function. This built-in function allows the pump to run at constant speed if the variable speed drive has failed or malfunctioned.
- Programmable analog and PWM outputs. These allow for feedback and monitoring devices.
- Networking capability. This allows for real-time monitoring and control from BMS, PLC, and other control systems.
- Reducing energy usage. Whether it is simply a case of reducing speed to suit the demand, automatically stopping a pump during periods of low flow rate or one of the drives specific energy saving functions, energy conservation is always a major consideration in pumping systems.
- Built-in PID control
- Torque vector control
- Password function
IMO HD2 VFDs can optionally be configured with a Programmable Logic Controller option card for added logic. With the built in PLC card or external, networked PLC the HD2 drives can be used for:
- Cascading pump control
- Dry pump protection, which is crucial should the pump run without enough water supply to prevent the pump from dry-running and damaging the bearing or motor.
- Anti-jam
- Check valve protection
- Slow flow rate protection
Find Your Variable Speed Booster Solution
As IMO Automation’s preferred control panel integrator for North America, Kerr Pump & Supply has the expertise to help you make the right variable speed booster pump solution for your water system. We have the capabilities to design control panels to meet your unique requirements for flow rate and pressure. Contact us for selection assistance in developing your variable speed booster pumping system.
article sponsored by IMO Automation and first appeared in PumpsandSystems.com October 2022.
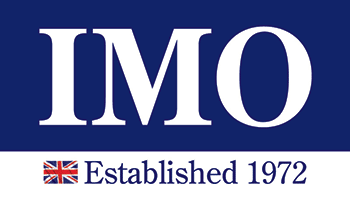